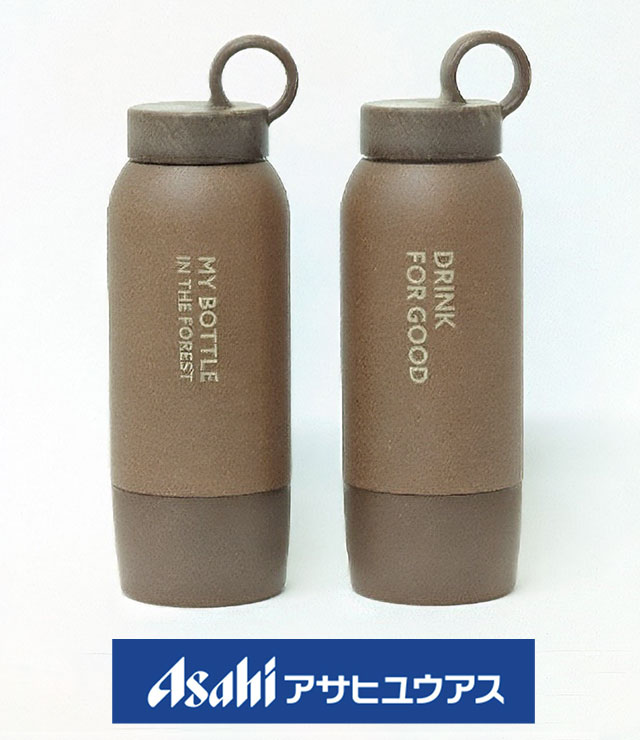
Notice
We exhibited at “Biocomposites Conference Cologne” held in Cologne, Germany, 6th- 7th December 2017, and got very popular. I thank you from the bottom of my heart.
We will post an English version leaflet of i-WPC.
Introduction
“i-CompologyTM” is a newly-coined word that abbreviates “Innovative · Composite · Technology.”
A composite material is formed by mixing different kinds of materials. (For example, “wood and plastic”, “metal and cement”, or “carbon fiber and plastic”)
In i-Compology, it is meaningful to establish new technologies that no one has been able to realize so far, and we are trying to innovate complex technology by using new methods.
As the first step, we will sell the next-generation wood plastic, which can be injection molded. It is made from wood powder and plastic. This wood plastic can be recycled. Also, when finally being incinerated as waste, CO2 emissions are very low. In other- words, this will material help preserve the global environment. (*1)
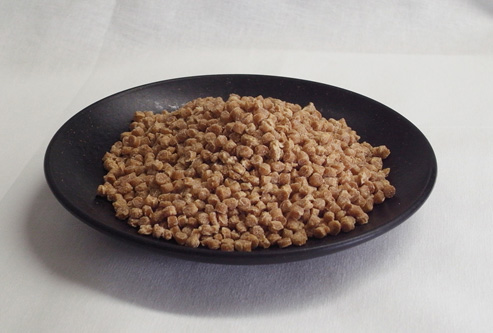
(*1) According to the carbon neutral concept, CO2 generated from burning a tree is not counted as an increase because it returns to nature again.
Injection moldable advanced wood plastic composite【i-WPC】
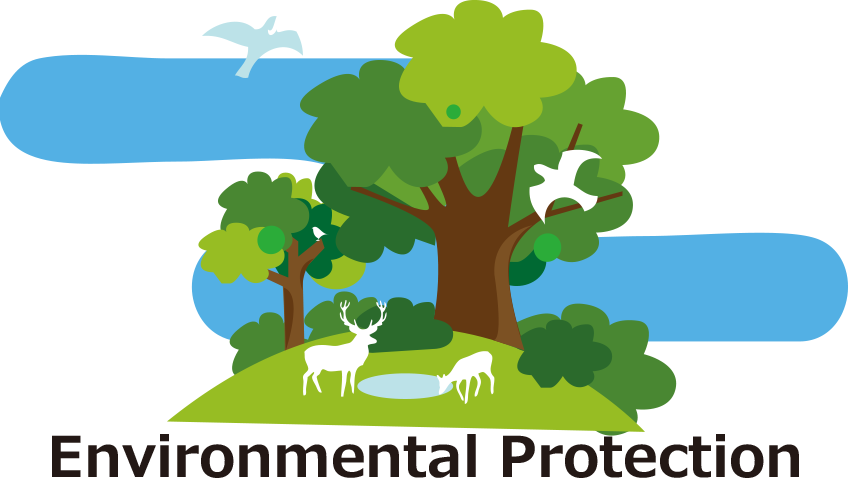
About “i-WPC”
Until now, composite materials of wood flour and plastic (wood plastic material, WPC) have been used in wood deck and park facilities as anti-septic woods, but they were manufactured in long bar-shape with same cross-sectional shape by the method called “extrusion molding”. On the other hand, there is a method suitable for mass-production called “injection molding”, that injects heat-melted resin into a metal mold as a method of making a form such as a bucket or a toy. But it has been considered remarkably difficult to injection mold with wood plastic composite, and there has been almost nothing produced commercially.
Usually, WPC’s melt viscosity is remarkably large, if you raise the molding temperature at 200℃ higher in order to reduce the melt viscosity, wood components will thermally decompose, resulting in bad odors and burns resulting in blackening. There are many difficulties to realize commercial production by injection molding. The manufacturing technology that we have established for WPC allows injection molding, which up to now has been regarded as impossible. “i-WPC” can be molded with general-purpose plastic injection molding machines and metal mold.
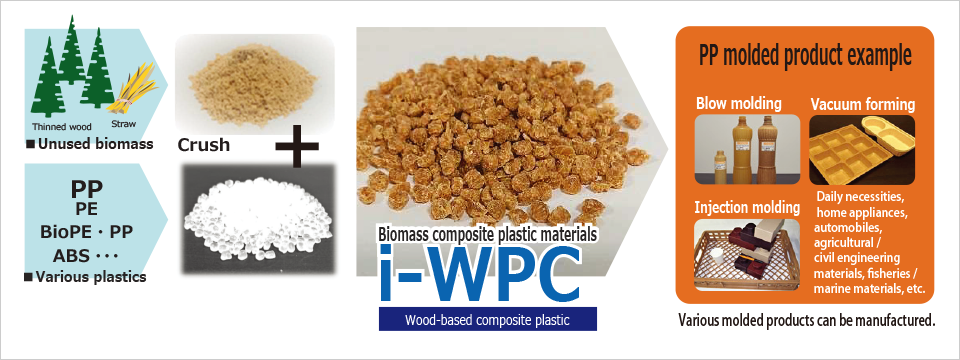
The features
Our WPC materials are higher elastic and more durable than the original plastics themselves, and, moreover, they can withstand high temperatures. Interestingly, rubbing the surface of a molded article with sandpaper can bond the molded article with adhesive (adhesion of polypropylene, etc. is generally difficult). There are also unique characteristics such as easy painting and low generation of static electricity.
Energy is necessary for pulverizing and mixing thinned wood, but energy for chemically treating and disassembling wood is not necessary, so there is also a merit in terms of manufacturing energy.
As a further important merit, we use wood powder made from thinned timber (*2) from forests, to help preserve Japanese forests. We will save a great deal of synthetic resin made from limited imported petroleum resources and use it as raw material not as fuel. Japanese forest resources surrounding us, including thinned timber, are available domestically,
(*2) For the purpose of properly maintaining artificial forests, thinning is necessary to secure sunshine in the forests. In the past, there was a demand for thinned timber to be used for scaffolding at construction sites and various woodworking products.
Recycling is also possible for this wood plastic material. When it becomes waste finally, it contains much wood flour, so it can be handled as burnable garbage. Also, there is drastically less CO2 generated by burning it compared with ordinary plastics, so it can reduce the burden on the global environment.
In short, “i-WPC” is a material originating in Japan that can contribute to conservation of forests in the world and CO2 emission reduction. It is our dream to use “i-WPC” as a solution to environmental problems and the needs of the world.
Summary of the features
- This material is superior to materials made only from plastic resins. It is higher elastic and more durable than plastics without wood powder and can withstand high temperatures. If the surface is rough, it can be bonded with adhesive. Static electricity in winter is also less likely to occur than with normal plastics.
- It can be easily pigmented or colored by painting. Also, you can get the feeling of the warmth of moist wood.
- It can be recycled. It can be disposed of with combustibles (*3). It is possible to reduce CO2 emissions significantly.
(*3) Conditions of combustibles vary depending on the regulations of the city, town, and village.
Test data
Test items | Test method | Unit | General-purpose Polypropylene | WPC, woodpowder31wt% | WPC, woodpowder51wt% | |
---|---|---|---|---|---|---|
Specific gravity | JIS K-7112 | – | 0.91 | 1.025 | 1.101 | |
Tensile test | Breaking strength | JIS K-7162 | Mpa | 35 | – | 35 |
Yield Strength | Mpa | 32 | – | |||
Elongation | % | – | 5 | <5 | ||
Bending test | Flexural strength | JIS K-7171 | Mpa | 41 | 46 | 55 |
Modulus of elasticity | Mpa | 1,350 | 2,000 | 3,570 | ||
Charpy impact test | Impact value | JIS K-7171 | kJ/㎡ | 3.3 | 2.9 | 3.3 |
Heat distortion temperature | 1.80M Pa | JIS K-7191 | ℃ | – | 71 | 94 |
0.45M Pa | ℃ | 100 | 115 | 130 |
The data described in this document are representative examples of measured values obtained under specified conditions and do not guarantee the physical properties of the application/product.
A-ha! Materials
Composite materials are not simply the combination of the properties of various materials. Depending on the combination method, there is a possibility of making a material that we had not realized could be made. (We call these “A-ha! Materials”.) For example, our founder commercialized a composite material of carbon black and polymer. At room temperature the electrical resistance is low and electricity flows, but when the temperature rises the electric resistance increases sharply. The electric resistance increases by one million times. This characteristic is called “positive temperature coefficient”, or “PTC”. Please try doing an Internet search for “Plathermo”. Since this material is made from plastics, it can be molded into a sheet. It is currently used for floor heating and even as an energy-saving electric heater that maintains a constant temperature on the entire surface of the sheet.
By using polymer composite technology, you might be able to develop various materials, such as light, thin, and strong sheets that replace steel plate, ultra-strong magnets whose shape can be freely changed, and sheets that quickly release heat.
Our business
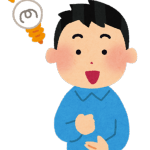
We create “A-ha! Materials.”
We will develop new complex technology and give shape to our dreams. You can anticipate something special. We will develop composite materials that give users intuitive ideas. In addition, we will create composite materials that users can easily understand in terms of the kinds of effect they have and why they have such characteristics. In the future, we would like to create something useful for the world by exercising creative ingenuity with users.